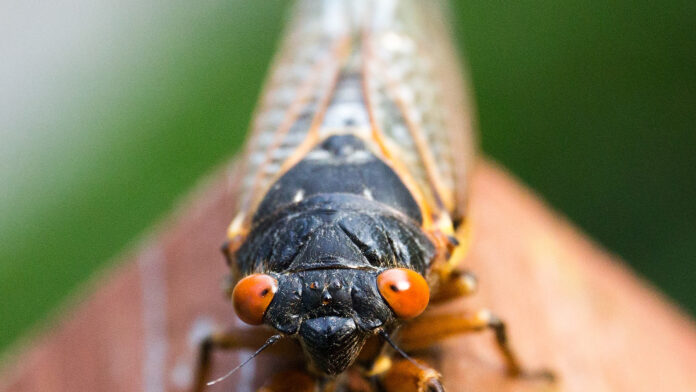
Discoveries in nature often inspire scientists to create things that benefit people. For example, the wings of the North American annual cicada – whose distinctive sound heralds the end of summer – are inhospitable to bacteria, antireflective, hydrophobic and provide camouflage.
“We often look to mother nature for interesting things. When scientists take a look at these things, it often involves the nanoworld,” said Kevin Walsh, associate dean of research and facilities, professor of electrical engineering at UofL’s J.B. Speed School of Engineering and founding director of UofL’s Micro/Nano Technology Center (MNTC).
Cicada wings’ antibacterial properties in particular interested University of Louisville engineers. Along with UofL biologists, the team analyzed the nanostructure of the insects’ wings and developed a nanofabrication technique to replicate it for potential use in spaces where bacteria are undesirable, such as food service, health care facilities and medical devices.
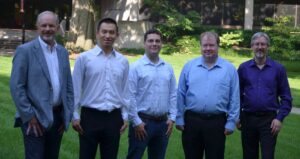
The team, led by Chuang Qu, Walsh and Mark Running, has developed a process to synthesize a surface material that mimics the wings’ structure and has the same antibacterial and water repellant properties as the wings that inspired it. The development and testing of the innovative manufacturing process was made possible through the use of state-of-the-art facilities at MNTC, which include a scanning electron microscope (SEM) and nanomaterial production capabilities.
With the help of an SEM, scientists can see that cicada wings’ surface consists of tiny, bowling-pin-shaped structures with a diameter of around 100 nanometers – about one-thousandth of the diameter of a human hair. The wings owe their antibacterial properties to the spike-shaped tops which act like daggers, piercing the cellular membranes of bacteria that have the misfortune of landing on them, ultimately killing the bacteria.
To replicate the cicada wings’ nanopillar cone structure, Qu, a senior research engineer at Speed School specializing in advanced nanofabrication, developed a two-step process of self-assembly and glancing-angle deposition (GLAD).
“All the structures we discovered under the microscope are challenging to recreate because they are so small and three-dimensional,” Qu said. “Using a two-step self-assembly plus glancing angle deposition, we were able to recreate the structure and confirm that, like their cicada wing template, they have these antimicrobial properties.”
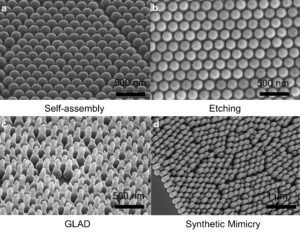
The manufacturing method consists of two processes. First, bases of the nanopillars are created using self-assembly, in which the material spontaneously falls into place. To create the tips of the bowling pin shapes, the researchers used GLAD, a technique in which physical vapor is deposited onto the base structure at an oblique angle. This procedure reduces the number of steps required to manufacture complex nanostructure materials that is cheaper and more scalable than other methods.
To verify the antibacterial effect of the nanostructure they had developed, the team tested it using E. Coli, common bacteria that have a fairly tough cell wall. Examining the effects of the manufactured surface on bacteria using the SEM at MNTC, the researchers found that the new material functioned in the same way as the cicada wings – destroying the bacteria with its dagger-like spikes.
Since the cicada wings and the replica material rely on physical nanostructures to kill the bacteria and can be made of virtually any material, the surfaces avoid possible negative effects of chemical antimicrobials in biomedical applications.
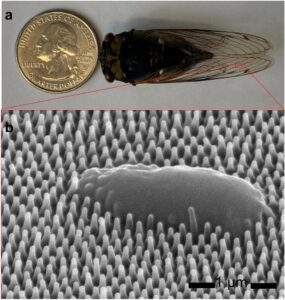
“We didn’t know it was going to be physical and that we would be able to detect it, so I was really happy that we were able to determine that,” said Mark Running, a UofL biology professor and coauthor of the published results in Scientific Reports.
While further work is needed to fully adapt the material to commercial use, it has potential for applications such as on doorknobs or other surfaces that need to be kept clean and germ free, food preparation surfaces and implantable medical devices that are prone to bacterial infection. The team has filed a provisional patent on a process called “inverted GLAD” to create materials such as the cicada wing replication and is seeking to hire students to assist with additional research.
“The challenges are how to scale the production up to larger areas and how to apply them to curved surfaces,” Walsh said. “Right now, we can just use it on flat surfaces.”
UofL’s MNTC facilities are available for use by researchers within and outside of UofL, as well as businesses conducting product research and development. It is one of 16 facilities at universities nationwide funded by the National Science Foundation to support research and industry. MNTC is one of eight advanced manufacturing facilities in the Kentucky MultiScale Manufacturing and Nanointegration Node, a consortium of resources at UofL and the University of Kentucky.