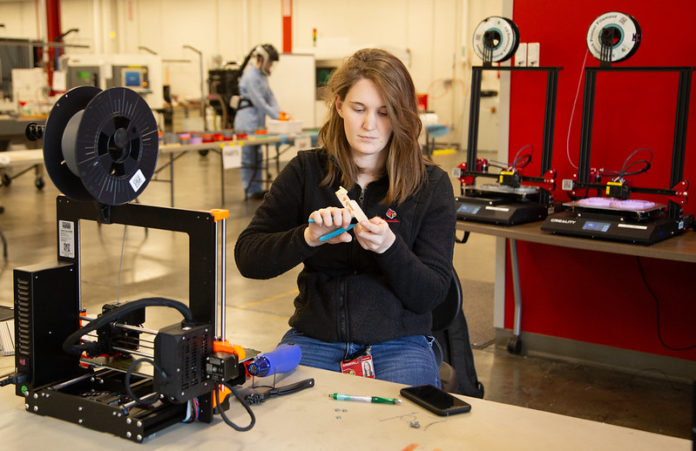
COVID-19 has caused a sea change in day-to-day life. Work, school, recreation, retail, medical care, everything has been altered.
Many have expressed a sense of frustration or helplessness because they feel there is nothing they can actively do to help – this virus is unprecedented. But for Speed School engineers at the University of Louisville, creating innovative solutions for the most complex problems – and taking action – is what they do best.
The Additive Manufacturing Institute of Science and Technology (AMIST) facility at Speed School of Engineering has risen to this challenge by contributing something vital to the pandemic: protective face shields for healthcare workers, an item currently in a critical shortage due to tightening of hospital supply chain lines. The original impetus for the project was a request for 100 of the shields from the Internal Medicine Department at UofL Health.
Created with state of the art 3-D printing technology, the team has been printing face shields at their core facility, increasing their production output to 55 shields per day by running continuous shifts from 8 a.m. to midnight daily.
Ed Tackett, director of Workforce Development at AMIST, is coordinating the COVID-19 Speed School Response Team.
“We asked ourselves, ‘what can we do right now?’ How do we protect our most vulnerable citizens and how can the University play a positive role in making that happen?” said Tackett. “We have medical professionals literally on the front lines, and if we can help them be safer or keep them from getting sick, we’re going to do whatever we need to do to make that happen,” said Tackett.
What he needed was a dedicated and talented production team. He got that team with graduate assistant Kate Schneidau and four other Speed School students who wanted to help however they could with this health crisis. Schneidau is the production manager who helps manage the scheduling of shifts totaling 16 hours a day, and ensures that builds are continuously running so they can output as many face shields as possible in a day.
Schneidau said she feels a sense of pride knowing that she is contributing skills she learned at Speed School in such a direct way to benefit the community.
“It’s more than just helping produce a product that can be sold commercially. It’s a sense of camaraderie with the community knowing in tough times I can still help. I was taught all my life if somebody needs help, you step up and help as much as you can without expecting anything, because it’s the right thing to do.”
The first batch of 100 face shields have been picked up, and while the face shield production is filling the gap until the medical supply chain catches up, the Additive Manufacturing center is nimble and can adapt quickly to new 3-D printing needs that may arise due to COVID-19.
“We’re producing face shields now but that could change at any moment,” said Schneidau. “We are here as a tool to help in whatever way the medical community may need. We could shift production to ventilators if that is what is needed next.”
The community is doing their part to help, too. After a post on social media about the project, citizens with 3-D printers have stepped up, wanting to be part of the solution. Schneidau has helped to coordinate drop-off locations for the components being printed by people with their home printers, and these parts are picked up and put in the production stream at Speed School.
Schneidau said this experience is one she won’t forget and, in fact, it has solidified her interest in a career in building medical devices.
“I want to make an impact to help people better their lives – to make sure they live their best life possible,” she said.
Tackett said with all the bad news every day about COVID-19, it is great having the team of students and other people involved in this.
“They feel like they’re making a difference, and they actually are making a difference. Students involved in this will be better equipped to provide significant engineering changes in the world. It’s what we should be doing as an engineering school. We’re all going to come out of this, and we’re all going to be stronger when we come out of this,” he said.
As for Schneidau, she is a millennial leader ready to keep making a difference in her world.
“The fact that these students have these skills and are willing to step up to the plate to help – this has just reaffirmed my belief that the next generation – we got it covered,” she said. “The future is in good hands.”
Check out the team’s work: